Welcome to our comprehensive guide on the curing times for new concrete, a crucial topic for homeowners and contractors alike in New Zealand. Understanding when you can safely drive on newly poured concrete is not only essential for maintaining the integrity of your investment but also for ensuring safety. In this article, we’ll explore everything from the basic curing process to the various factors that influence how long you should wait before using your new driveway or pavement. Whether you’re dealing with the temperamental NZ climate or working with different concrete mixes, we have you covered with expert advice and tips to ensure your concrete sets perfectly.
In New Zealand, the general recommendation is to wait at least 7 days before driving on new concrete. However, this can vary based on factors like the concrete mix used, the thickness of the pour, local climate conditions, and whether any accelerators were added to the concrete. For standard residential driveways, waiting 7 to 28 days allows the concrete to achieve sufficient strength to withstand vehicular traffic without damage. For the best results, consult with a local concrete professional to consider specific conditions in your area.
Table of Contents
Understanding Concrete Curing
Concrete curing is a vital process in construction that ensures newly poured concrete reaches its maximum strength and durability over time. When concrete is first mixed and poured, it’s in a liquid state, containing water, cement, and aggregates like sand and gravel. As it dries, the water reacts chemically with the cement in a process known as hydration, which binds the aggregates together and gradually hardens the mixture into solid concrete. This transformation, while seemingly straightforward, is influenced by a range of environmental and material factors and can significantly impact the concrete’s final properties.
Why Concrete Curing is Crucial
The primary reason concrete curing is crucial lies in its impact on the structural integrity and longevity of the concrete structure. Properly cured concrete is significantly more resistant to environmental stresses such as freeze-thaw cycles, moisture, and heat. Without adequate curing, concrete can become brittle, weak, and more susceptible to premature cracking and other types of degradation. This can lead to a shortened lifespan of concrete structures and increased maintenance costs over time.
Curing is not merely a waiting game; it’s an active process that requires maintaining optimal conditions to ensure the concrete develops its intended strength and durability. This involves controlling the moisture content and temperature of the concrete during the early stages of hydration. If the concrete dries too quickly, the hydration process can halt prematurely, weakening the structure. Therefore, methods such as wet burlap coverings, plastic sheeting, or spraying curing compounds are used to retain moisture in the concrete during the critical curing period.
The Science Behind Concrete Curing
Understanding the scientific aspects of concrete curing provides deeper insight into how concrete gains strength over time. The strength of concrete is directly tied to the progress of the hydration reaction between water and cement. During hydration, the cement particles react with water to form new compounds, most notably calcium silicate hydrate, which serves as the primary binder holding the aggregates together. This process releases heat, known as the heat of hydration, and continues over time, significantly contributing to the concrete’s strength development.
The rate of hydration, and thus the development of strength, is influenced by several factors.
- Temperature: Higher temperatures generally speed up the hydration process but can also lead to faster moisture loss. Maintaining a moderate temperature is key to optimal curing.
- Water-Cement Ratio: The proportion of water to cement in the mix also affects the curing process. Too much water can weaken the structure, while too little can inhibit complete hydration.
- Concrete Composition: Additives and admixtures can alter the rate of hydration and the physical properties of the concrete. For example, accelerators can speed up the curing process, which is useful in colder weather.
The science behind concrete curing reveals why careful attention to curing practices is essential for ensuring that concrete structures are durable, safe, and long-lasting. By understanding and controlling the hydration process, constructors can enhance the performance of concrete, tailoring it to meet the specific demands of various building projects and environmental conditions.
Concrete curing is a foundational aspect of construction that affects everything from the concrete’s practical usability to its longevity and structural integrity. Ensuring proper curing practices are followed is not just about following regulations; it’s about building infrastructures that stand the test of time. By fostering a deeper understanding of this process, we can improve construction quality and outcomes across the industry.
When considering the curing times for new concrete, it’s crucial to adhere to general guidelines and specific industry standards to ensure the structural integrity and longevity of the concrete. This section delves into the standard curing times for concrete, focusing on practices and expectations within New Zealand.

Standard Curing Times For Concrete
Concrete curing is a critical process that begins as soon as the concrete is poured and lasts until it reaches a sufficient level of hardness to handle its intended load. The standard curing time refers to the period during which concrete gains strength and durability through the process of hydration, where water reacts with cement.
General Guidelines on Curing Times for Concrete
The general guideline for curing concrete is that it should not be subjected to any significant load until it has achieved at least 70% of its intended strength. Typically, concrete takes about 28 days to reach 90% of its full strength, which is considered sufficient for most types of loads. However, initial curing stages are critical, and specific milestones must be respected to avoid damage.
- 24 to 48 hours – Concrete can be walked on without impacting its surface integrity.
- 7 days – Concrete can support vehicle traffic, assuming standard environmental conditions and mix designs.
- 28 days – Concrete should have reached its specified compressive strength, suitable for heavy loads and fully operational use.
It’s important to note that these times can vary based on the type of concrete mix used, environmental conditions, and the specific additives or accelerators included in the mix.
Industry Standards in New Zealand
In New Zealand, the industry standards for concrete curing times align with global best practices but also take into account local environmental factors. The New Zealand Concrete Society provides guidelines that are widely accepted within the local construction industry, emphasizing the need for a minimum of 7 days of keeping the concrete moist to facilitate the curing process. This practice helps prevent premature drying, which can lead to cracking and weakened structures.
The New Zealand Building Code also stipulates that concrete must meet specific strength requirements before being subjected to load, which usually aligns with the 28-day curing period for standard concrete mixes. However, for faster project timelines or specific structural requirements, contractors may use high-early-strength concrete that accelerates the curing process, reducing the wait time before the concrete can bear significant loads.
Adhering to the standard curing times and industry guidelines is essential for any construction project involving concrete in New Zealand. By allowing concrete to cure properly, it gains the strength and durability needed to perform its function safely and effectively over its intended lifespan. Contractors and DIY enthusiasts alike should always consult the latest guidelines from local authorities and material suppliers to ensure compliance and optimal results.
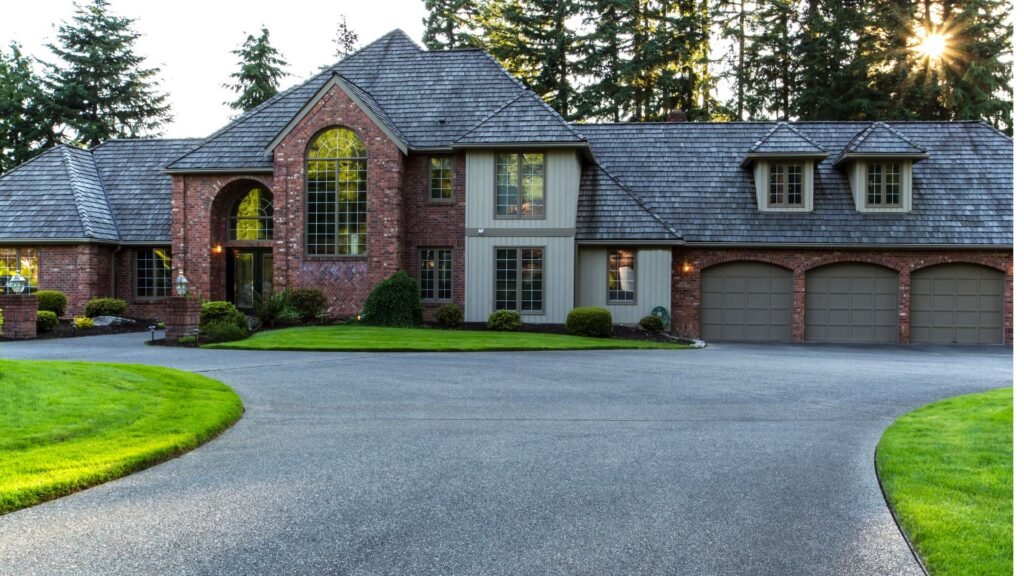
Factors Influencing Curing Time
When it comes to setting new concrete, understanding the factors that influence curing time is crucial for achieving optimal results. Here in New Zealand, with its unique climatic conditions and varied applications, several key elements must be considered to ensure your concrete installations are both durable and functional. Let’s delve into how temperature and climate, humidity levels, concrete mix, and the thickness and type of application play pivotal roles in the curing process.
Temperature and Climate
New Zealand’s climate varies dramatically from the subtropical North to the temperate South, and these regional differences significantly impact concrete curing times. Warmer temperatures generally speed up the curing process, as the chemical reactions that strengthen concrete occur faster at higher temperatures. Conversely, cooler temperatures slow down these reactions, extending curing times. For instance, concrete poured during a warm Northland summer might cure quicker than the same concrete in the cooler, damper conditions of Southland’s winter. It’s important to monitor the weather forecast and plan your concrete projects accordingly, perhaps even adjusting your schedules to avoid extremes that could impair the curing process.
Humidity Levels
Humidity plays a crucial role in the concrete curing process. Concrete needs moisture to cure effectively; too little humidity and the concrete may dry too quickly, risking cracks and weakness. Too much moisture in the air, however, can slow down the curing process by preventing the water in the concrete from evaporating at a normal rate. In coastal areas of New Zealand, where humidity tends to be higher, concrete installations may require adjustments in the mixture or protective measures like curing covers to maintain an optimal moisture level during the curing phase.
Concrete Mix
The choice of concrete mix can greatly influence curing times. Standard concrete mixes typically require about 28 days to reach full strength, whereas rapid-set concrete mixes might be ready for light traffic in less than half that time. The components of the mix, such as the type and amount of cement or additives like fly ash or slag, also affect how quickly concrete reaches its initial and final set. For projects where time is of the essence, choosing a rapid-set mix might be beneficial, but it’s vital to consider the specific needs of the project—rapid-set mixes might not always be suitable for all types of loads or finishes.
Thickness and Type of Application
The thickness of the concrete and its intended use also significantly affect curing times. Thicker pours, such as those used for commercial roadways or industrial platforms, naturally take longer to cure due to the larger volume of concrete and its ability to retain moisture longer. In contrast, thinner applications like residential driveways or walkways may cure faster. The intended use also dictates the type of concrete mix and curing process to be used. For example, a commercial roadway needs to withstand heavier loads and more wear and tear, requiring a stronger, more durable mix that might need a longer curing time to achieve optimal strength and longevity.
By understanding and managing these factors, you can ensure that your concrete installations in New Zealand not only cure properly but also stand the test of time, providing safe, durable surfaces for everything from private driveways to public roads. Always consider the specific conditions of your project and consult with professionals when in doubt to achieve the best results.

The Role Of Sealers And Curing Compounds
When it comes to enhancing and protecting your newly poured concrete, sealers and curing compounds play a pivotal role. Understanding what these products are and how they benefit your concrete installation can ensure longevity and durability, especially in the variable climates of New Zealand.
What are Sealers and Curing Compounds?
Sealers are protective coatings applied to concrete to prevent the penetration of moisture and contaminants such as oil, chemicals, and salts, which can cause damage over time. They form a barrier on the surface, which not only protects but also enhances the appearance of the concrete. On the other hand, curing compounds are specifically designed to facilitate the proper curing of concrete. They form a moisture-retentive film over the surface of freshly poured concrete, which helps maintain adequate moisture content during the crucial early stages of strength development.
Benefits of Using These Products
The primary benefit of using sealers and curing compounds is the significant extension of the concrete’s lifespan and enhancement of its durability. By retaining essential moisture, curing compounds ensure that the concrete cures uniformly and achieves its maximum potential strength, reducing the risk of cracks and other structural flaws. Sealers provide added protection against environmental factors and staining, which is particularly important in areas exposed to harsh weather conditions and frequent usage. Together, these products can dramatically reduce maintenance costs and enhance the visual appeal of the concrete surface, making it a wise investment for any concrete application.
Recommendations for Products Available in New Zealand
In New Zealand, several reputable products can provide excellent protection and curing for your concrete. For curing compounds, products like Sika Antisol or BASF MasterKure are highly recommended by professionals for their reliable performance. These are readily available through most major building supply stores across the country. As for sealers, consider using brands like Dulux Avista or Resene Concrete Sealer, which offer a range of options depending on the finish and protection level you desire. It’s advisable to choose a product that aligns with the specific needs of your project, such as UV resistance for outdoor applications or enhanced durability for high-traffic areas.
Choosing the right sealer and curing compound can be as crucial as the concrete mix itself. Therefore, it’s recommended to consult with a local specialist who can provide advice tailored to the New Zealand environment and your particular project requirements. Implementing these products not only preserves the integrity of your concrete but also ensures that it remains a functional and aesthetic part of your property for years to come.
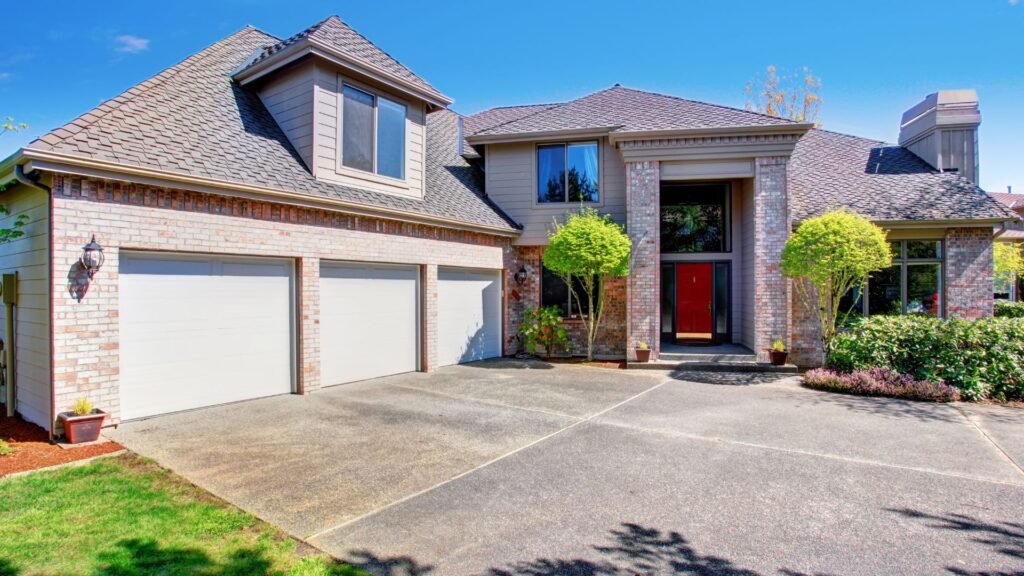
How To Test If Concrete Is Ready
Determining whether your new concrete is ready to endure the weight of vehicles or foot traffic without sustaining damage is crucial. This section explores both DIY methods and professional assessments to help you gauge the readiness of concrete, ensuring that you apply the most suitable techniques for your situation.
Tools and Methods to Determine the Concrete’s Readiness for Use
One of the primary tools used by professionals to test concrete strength is the maturity meter. This device measures the temperature history of the concrete to predict its compressive strength. Another professional tool is the Windsor probe, which uses a spring-driven pin to penetrate the concrete surface, providing a direct measure of the compressive strength.
For those preferring a less technical approach, a simple and effective method is the press test. By pressing a sharp object like a nail or screwdriver into the concrete, you can assess its hardness. If the object leaves only a slight impression or none at all, the concrete is generally considered ready for light use.
DIY Methods vs. Professional Assessments
DIY methods can be useful for small-scale projects where precision is not the highest priority. Alongside the press test, another common DIY method is the curing time estimation. Most concrete mixes provide specific guidelines on how long the concrete should cure before it’s ready for use, typically ranging from 7 to 28 days depending on the mix and environmental conditions.
However, for larger projects or when precision is crucial, professional assessments are recommended. Professionals use advanced tools and their expertise to provide a more accurate assessment of concrete readiness. This is particularly important in environments where safety or significant financial investment is at stake.
Testing whether concrete is ready for use is a vital step in any construction project. While DIY methods can provide a general sense of readiness, professional assessments offer accuracy and peace of mind, especially in critical applications. Choosing the right method depends on the scale of your project, your expertise, and how critical the concrete’s performance is to your overall project success.
Incorporating these methods into your project planning will ensure that your new concrete installation maintains its integrity and longevity, ultimately saving you time and money in repairs and maintenance. Whether you opt for a simple press test or a full professional assessment, understanding the readiness of your concrete is key to a successful project.
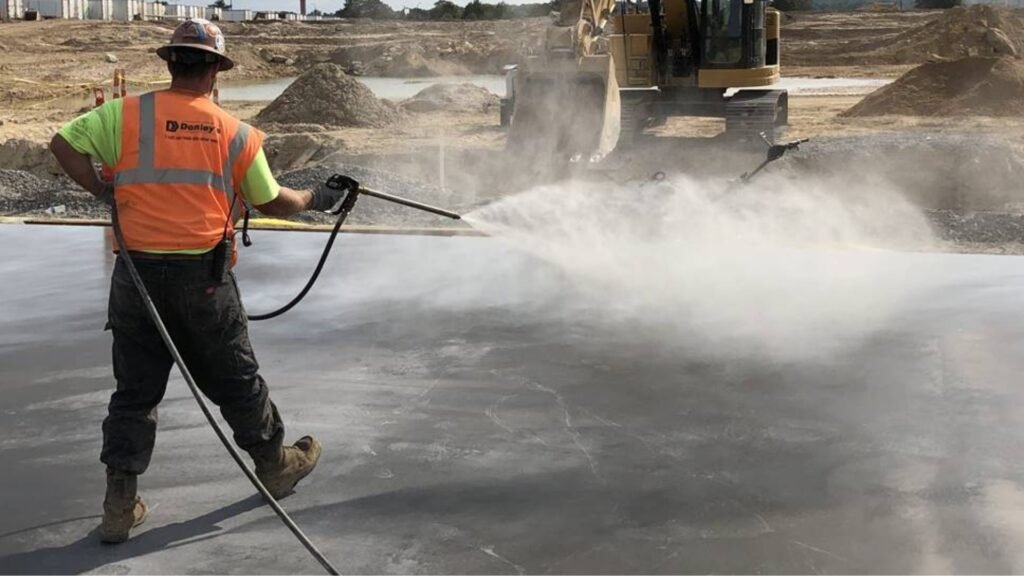
Tips For Faster Curing
When dealing with concrete installations, time is often of the essence. Whether you’re setting up a new driveway or laying down a commercial parking lot, speeding up the curing process can save valuable time and reduce the period before the concrete is fully functional. However, it’s crucial to approach this process carefully to maintain the strength and durability of the concrete. Here are some practical tips and important do’s and don’ts during the initial curing phase to expedite concrete curing without compromising its integrity.
Practical Tips to Speed Up Concrete Curing
1. Use a Curing Accelerator: Adding curing accelerators to the concrete mix is one of the most effective ways to speed up the curing process. These additives are designed to reduce the setting time and increase the rate of strength gain. This is particularly useful in cooler climates or when quick serviceability is required. Be sure to consult with a concrete professional to choose the right accelerator that won’t adversely affect the concrete’s long-term performance.
2. Apply Heat and Control Moisture: Maintaining a warm and moist environment helps concrete cure faster. Covering the concrete with curing blankets or plastic sheeting can trap heat and moisture, accelerating the curing process. In colder months, heated enclosures or electric curing blankets may be used to maintain optimal curing temperatures.
3. Opt for Warm Mixes: Using warm water or aggregates during the mixing process can significantly reduce curing time, especially in colder weather. The increased temperature of the mix promotes faster chemical reactions within the concrete, enhancing strength development early on.
Do’s and Don’ts During the Initial Curing Phase
Do’s
- Do Keep the Concrete Moist: One of the critical factors in curing concrete is keeping it moist. Use water sprays, wet burlap, or hydrophilic covers to prevent the concrete from drying out too quickly, which can lead to cracking and weakened surfaces.
- Do Use Quality Materials: Always ensure that your concrete mix is sourced from reputable suppliers. High-quality materials can dramatically improve the efficacy of the curing process and the overall durability of the concrete.
- Do Protect from Extreme Weather: Shield the concrete from extreme elements—sun, wind, and rain can hinder the curing process. Strategic placement of barriers or covers can protect the concrete and aid in maintaining a consistent temperature.
Don’ts
- Don’t Rush the Process: While it’s tempting to expedite the curing, rushing can lead to subpar results. Avoid putting any weight or stress on the surface before the recommended time.
- Don’t Neglect Temperature: Ignoring the temperature of the concrete and the environment can lead to poor curing. Concrete that freezes soon after being poured may never reach its optimal strength.
- Don’t Skimp on Curing Time: Even when accelerators are used, give the concrete enough time to develop its intended strength. Cutting corners can lead to structural failures and increased maintenance costs down the line.
Incorporating these tips into your concrete curing process can ensure that you achieve a hardy, durable surface ready for use in a shorter amount of time. Always balance the need for speed with the need for quality and durability to get the best results from your concrete installation.
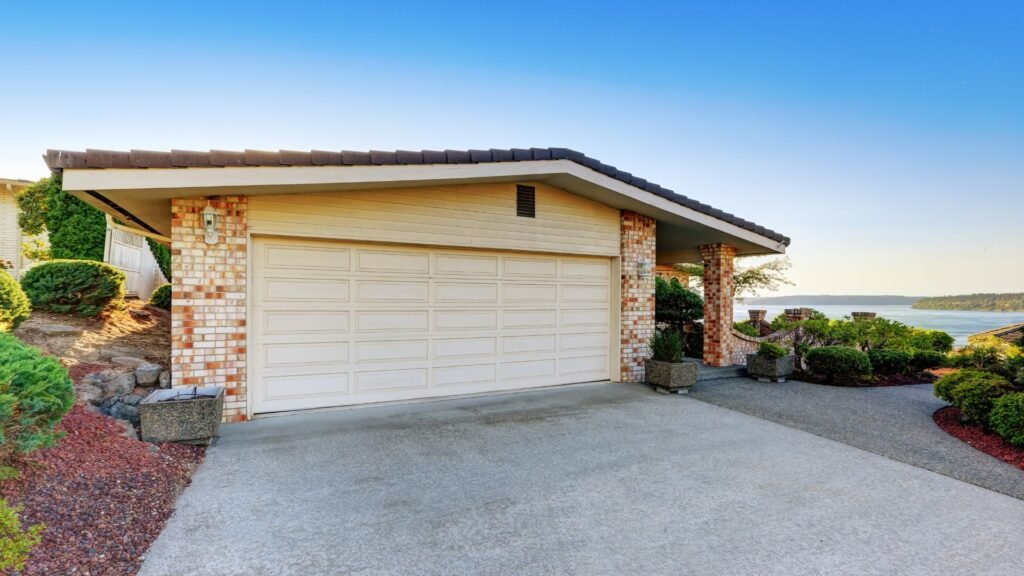
The Consequences Of Premature Loading On New Concrete
When it comes to new concrete installations, whether it’s a driveway, walkway, or any structural foundation, the importance of allowing proper curing time cannot be overstated. Curing concrete is not just a waiting game—it’s a critical phase in the lifespan of the material that ensures it reaches its full strength and durability. Despite this, one common misstep often made is premature loading, or subjecting the concrete to weight and traffic before it has sufficiently hardened. Understanding the potential risks and long-term consequences of such actions can save property owners significant time and money while also preventing safety hazards.
Potential Damage and Safety Issues
The immediate consequence of driving or placing heavy loads on concrete that hasn’t fully cured is visible damage. This might manifest as cracks, which can appear small initially but widen over time, or surface crumbling where the concrete simply can’t withstand the pressure. Not only does this compromise the look of your new installation, but it also raises serious safety concerns. For instance, uneven surfaces and cracks pose tripping hazards, and in areas that bear significant loads, like driveways or industrial floors, these compromised areas can lead to more severe structural failures that may result in accidents or injuries.
Long-Term Effects on Durability and Surface Integrity
Premature loading affects more than just the surface appearance of the concrete. Internally, the concrete continues to hydrate and gain strength long after it appears dry. Interrupting this process can lead to a reduced lifespan for the concrete. Areas subjected to early loading often show premature aging, which includes not only an increase in crack propagation but also greater susceptibility to weather-related damage such as frost heave or water penetration.
Water is a particular enemy of improperly cured concrete because it can enter through cracks and micro-fractures, freeze, and expand, thus exacerbating the damage. This moisture ingress can lead to further weakening of the concrete’s internal structure, increasing the likelihood of flaking and spalling. Furthermore, the compromised concrete is less able to resist the penetration of oils, chemicals, and other substances that can degrade its composition, leading to costly repairs and maintenance.
The key to preventing these issues lies in planning and patience. Allow concrete to cure for the recommended duration—typically a minimum of 7 days for residential projects, and potentially longer for commercial applications or during colder weather. Consulting with a professional to understand the specific needs of your concrete mix and environmental conditions can also guide your decision-making process.
Ultimately, taking the time to ensure your concrete has properly cured before applying any load will protect your investment, enhance safety, and extend the surface’s functional lifespan. This attention to detail will result in a more durable, resilient concrete installation that meets both current and future needs without unforeseen complications.
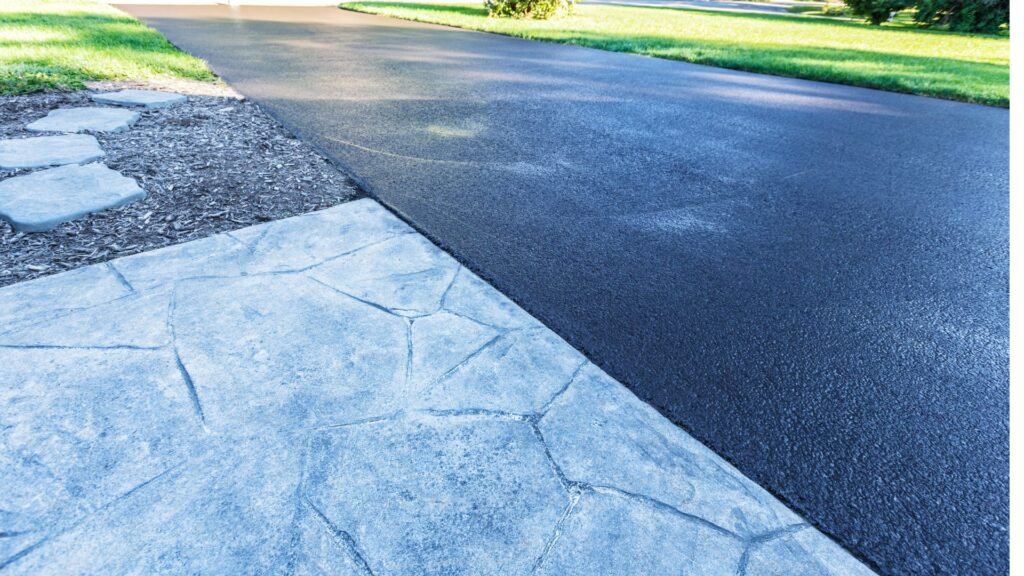
Maintenance Tips For New Concrete
Maintaining new concrete is crucial for ensuring its longevity and durability. Whether you’ve just paved a driveway, laid a patio, or poured a new sidewalk, taking the right steps early on can help prevent damage and preserve the surface’s integrity over time. Here’s a detailed guide on best practices for maintaining new concrete and how regular care can significantly extend its life.
Best Practices for Maintaining New Concrete
1. Proper Curing: One of the most critical steps in maintaining new concrete is ensuring it cures properly. Curing concrete involves maintaining adequate moisture and temperature to allow the concrete to gain strength effectively. For the first seven days after pouring, it’s important to keep the concrete moist using curing blankets, plastic sheeting, or regular misting, especially in dry and windy conditions.
2. Apply a Sealer: After the concrete has cured (usually after 28 days), applying a high-quality sealer can provide an extra layer of protection. Sealers help protect against moisture absorption, chemical corrosion, and stain penetration. Depending on exposure conditions and traffic levels, reapply the sealer every 2 to 5 years.
3. Clean Regularly: Regular cleaning is vital to maintain the appearance and safety of concrete surfaces. Sweep off dirt, leaves, and other debris to prevent staining and deterioration. For tougher stains, mild detergent and a pressure washer can be used sparingly to keep the surface clean without causing damage.
4. Avoid Deicers: In colder climates, avoid using deicing chemicals during the concrete’s first winter. The chemicals can cause rapid freeze-thaw cycles that may damage immature concrete. Instead, use sand for traction. If deicers are necessary in subsequent winters, opt for products that are less harsh and more concrete-friendly.
5. Control Load: Avoid putting excessive weight on new concrete. While concrete is an incredibly durable material, excessive loads early on can cause cracks and other structural damages. This is especially important in the first month after pouring when the concrete is still gaining strength.
How Regular Maintenance Extends the Life of Concrete Surfaces
Regular maintenance not only keeps your concrete looking new but also extends its lifespan by preventing the most common causes of deterioration.
- Preventing Cracks: Regular sealing and proper load management help prevent cracks. Once cracks form, they can allow moisture and chemicals to penetrate deeper into the concrete, which accelerates the deterioration process.
- Avoiding Discoloration and Surface Wear: Frequent cleaning helps avoid the buildup of substances that can stain or etch the concrete surface. By keeping the surface clean, you also reduce wear from abrasives like dirt and sand.
- Enhancing Structural Integrity: By maintaining an optimal balance of moisture and protecting the surface from extreme temperatures and chemicals, regular maintenance ensures that the concrete continues to cure and gain strength over time.
- Mitigating Freeze-Thaw Damage: In colder regions, managing how the concrete interacts with moisture and temperature changes is crucial. Well-maintained concrete is less susceptible to the damaging effects of freeze-thaw cycles.
By following these maintenance tips, you can ensure that your new concrete installation retains its strength, functionality, and aesthetic appeal for many years to come. Regular care not only protects your investment but also enhances the value of your property by keeping its exterior in excellent condition.
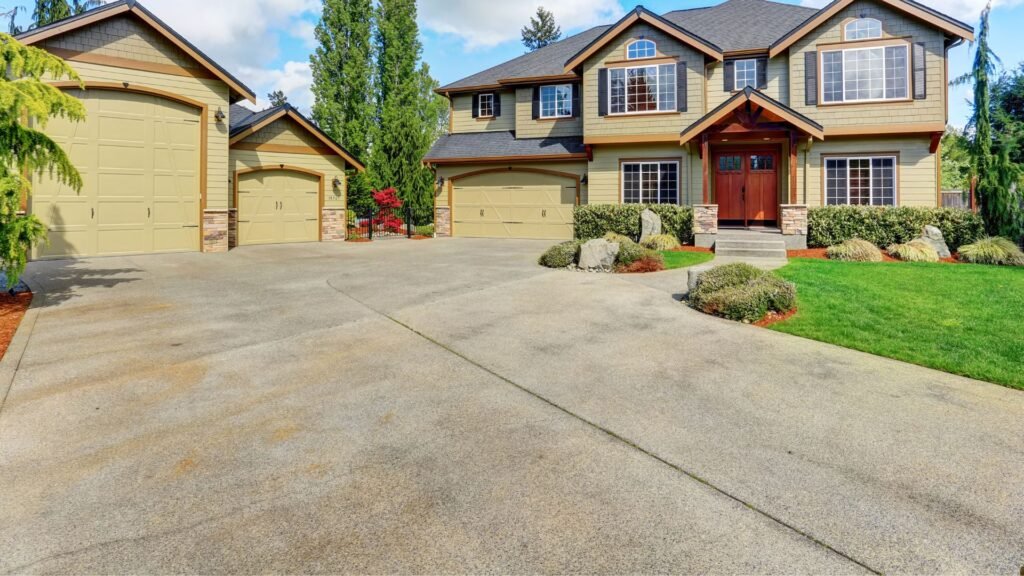
FAQs: About How Long Before You Can Drive On New Concrete NZ
What is the minimum recommended waiting time before driving on new concrete in New Zealand?
The minimum recommended waiting time is typically 7 days. This allows the concrete to achieve sufficient strength to handle the weight of a vehicle without sustaining damage.
Does the type of vehicle affect how long I should wait before driving on new concrete?
Yes, heavier vehicles require a longer curing time due to the increased pressure they exert on the concrete. For light passenger vehicles, 7 days may suffice, but heavier vehicles might require waiting up to 28 days.
How does the weather affect concrete curing times?
Weather conditions significantly impact curing times. Cold weather can slow down the curing process, requiring a longer wait time, while warm, humid conditions can accelerate it. Always consider the specific weather conditions when determining the curing time.
Can I use any additives to speed up the curing process?
Yes, there are additives and accelerators that can be mixed into the concrete to speed up curing times. However, consult with a professional before using these, as they might affect the final strength and durability of the concrete.
What are the risks of driving on concrete too soon?
Driving on concrete before it has fully cured can lead to cracks, surface damage, and structural weaknesses that compromise the longevity and safety of the concrete.
How can I tell if the concrete is ready to be driven on?
Professional assessment is best, but signs like the concrete’s ability to withstand pressure without marking are indicators. DIY methods like pressing into the concrete with a heavy object can also help determine surface hardness.
Are there specific signs of concrete that is not ready to handle vehicle traffic?
Yes, if the concrete feels soft, looks wet, or easily indents when pressure is applied, it is not ready for vehicle traffic.
How does concrete mix influence curing times?
Different concrete mixes have different curing times. For instance, quick-setting concrete can cure faster than standard mixes. The specific composition and any additives can alter how quickly concrete reaches its full strength.
What maintenance should be performed on new concrete during the curing period?
During curing, it is important to keep the concrete moist and avoid any activities that could stress the concrete, such as heavy loads or sharp impacts. Regular checks for cracks or other signs of distress should be conducted.
Can I walk on new concrete before the period to drive on it has passed?
Walking on new concrete can generally be done after 24-48 hours post-pour, much earlier than the time required to support vehicles, but always check with your concrete provider for specific guidance based on your concrete mix and environmental conditions.
Conclusion
In conclusion, understanding the proper curing time for new concrete is crucial for ensuring its longevity and structural integrity. Throughout this article, we’ve covered essential aspects such as the general guidelines for curing times, the impact of various factors like climate, concrete mix, and application type, and the importance of using sealers and curing compounds. Remember, while the standard recommendation is to wait at least 7 days before driving on new concrete, factors specific to New Zealand’s environment can alter this timeframe. For the best outcomes, it’s vital to consult with concrete professionals and adhere to local building codes and guidelines. By following expert advice and maintaining patience during the curing process, you ensure that your concrete installation remains durable and safe for years to come.
About the Author:
Mike Veail is a recognized digital marketing expert with over 6 years of experience in helping tradespeople and small businesses thrive online. A former quantity surveyor, Mike combines deep industry knowledge with hands-on expertise in SEO and Google Ads. His marketing strategies are tailored to the specific needs of the trades sector, helping businesses increase visibility and generate more leads through proven, ethical methods.
Mike has successfully partnered with numerous companies, establishing a track record of delivering measurable results. His work has been featured across various platforms that showcase his expertise in lead generation and online marketing for the trades sector.
Learn more about Mike's experience and services at https://theleadguy.online or follow him on social media: