Welcome to our comprehensive guide on understanding how thick the concrete in a car park should be in Auckland. While it’s easy to overlook, the thickness of concrete plays a crucial role in ensuring the durability, safety, and longevity of any parking structure. Whether you’re curious about the specifics of a residential driveway or a commercial car park, knowing how factors like traffic load, soil conditions, and Auckland’s unique weather patterns influence concrete thickness is essential. In this post, we’ll explore the key considerations behind car park construction, offering insights that help you understand why a solid foundation is more than just concrete it’s a careful balance of science, regulations, and smart design choices tailored for Auckland’s environment.
The standard concrete thickness for a car park in Auckland typically ranges from 100mm to 200mm, depending on factors such as traffic load, soil conditions, and drainage requirements. For light vehicle traffic, a 100mm slab may suffice, while heavier traffic, like delivery trucks, may require up to 200mm for added durability and support. Local building codes and Auckland’s weather conditions also play a significant role in determining the appropriate concrete thickness to ensure long-term performance.
Table of Contents
General Standards For Car Park Concrete Thickness
Basic Guidelines
When designing and constructing a car park, one of the key considerations is the appropriate concrete thickness. Typically, car park concrete thickness ranges between 100mm to 200mm. However, the exact thickness varies depending on several factors, including the anticipated load and type of traffic that will use the space.
For light vehicles, such as personal cars or small vans, a thickness of 100mm to 150mm is usually sufficient. On the other hand, for areas where heavier vehicles, such as delivery trucks or buses, frequently operate, the concrete should be thicker, ideally around 175mm to 200mm. This variation ensures that the car park can handle the specific stresses applied by different vehicles, reducing the risk of cracks and structural failure over time.
Why It Matters
The thickness of concrete in a car park is not just a structural consideration; it plays a critical role in the durability, performance, and maintenance requirements of the space.
1. Longevity: A thicker concrete layer helps enhance the overall lifespan of the car park. Thinner slabs might initially suffice but are more prone to wear and tear, leading to more frequent repairs. Investing in the appropriate concrete thickness from the outset can result in long-term cost savings by minimizing the need for constant maintenance or early resurfacing.
2. Load-bearing Capacity: As the primary foundation for vehicles, the concrete thickness directly impacts how much load the surface can bear. A car park designed for standard passenger cars doesn’t need the same thickness as one used by heavier commercial vehicles. By matching the thickness to the expected load, the risk of cracking, warping, or other damage is significantly reduced, ensuring a safer environment for users.
3. Maintenance: Thicker concrete provides better resistance to environmental factors such as water penetration, temperature fluctuations, and general wear and tear. A car park with inadequate thickness is more likely to develop cracks and potholes, which lead to higher maintenance costs over time. In contrast, a well-constructed car park with appropriate concrete thickness requires fewer repairs and remains in better condition for longer.
Ultimately, choosing the right concrete thickness for your car park enhances its strength, durability, and cost-effectiveness, ensuring it remains functional and safe for years to come.
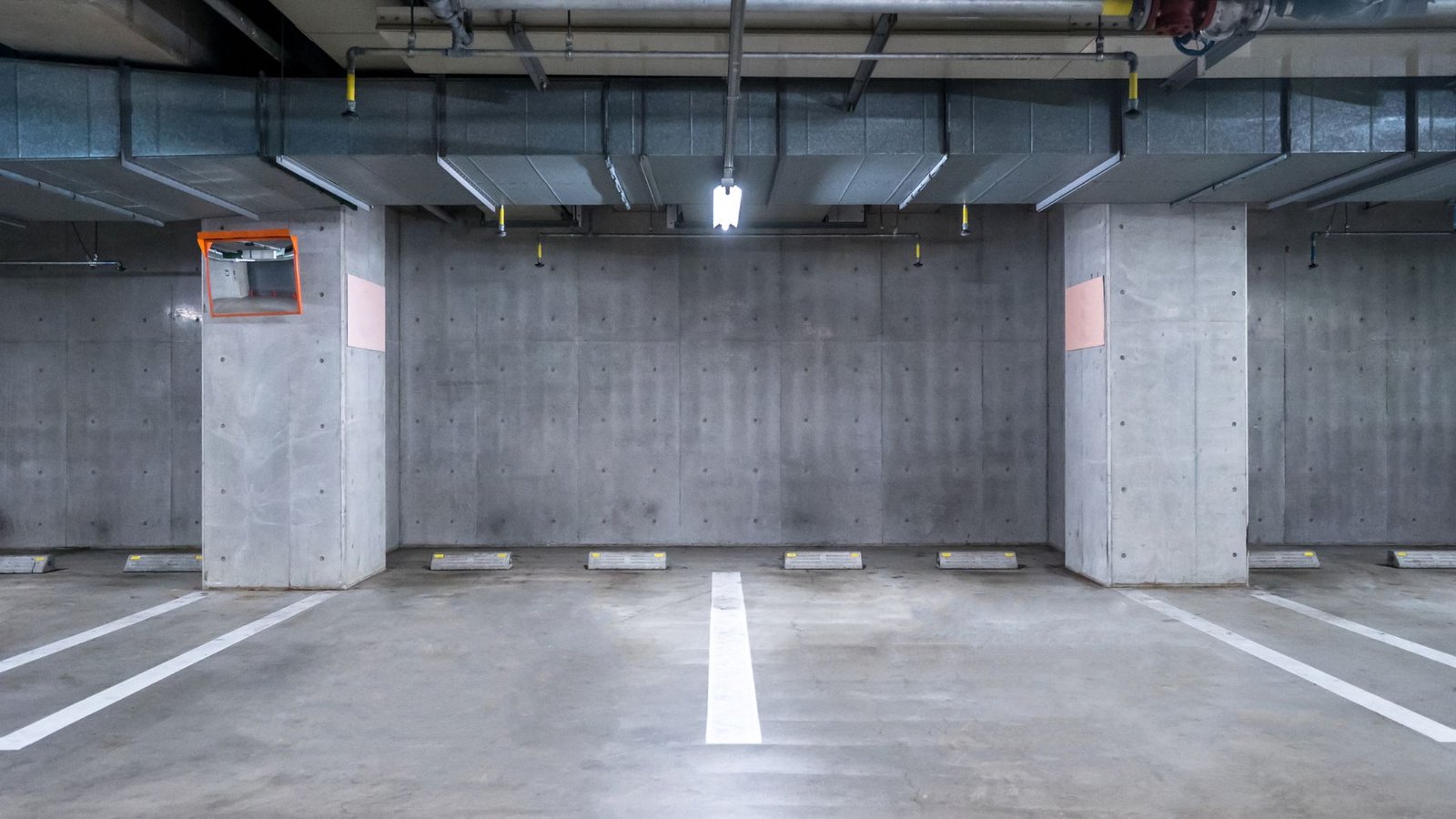
Factors That Affect Concrete Thickness In Car Parks
When designing car parks, particularly in regions like Auckland, several factors influence the required concrete thickness. Each of these variables plays a key role in ensuring the car park is both durable and functional over time. In this section, we’ll explore how traffic load, geological conditions, weather, and drainage impact the thickness of concrete in car parks, especially in the Auckland area.
Traffic Load
One of the most important factors that determine the thickness of concrete in car parks is the type of traffic the structure is expected to handle.
- Light vs. Heavy Traffic: Car parks intended primarily for passenger vehicles, such as sedans or SUVs, generally require less concrete thickness compared to those that accommodate heavier vehicles like delivery trucks, buses, or construction equipment. For light-traffic car parks, a thickness of around 100mm to 150mm is typically sufficient. However, areas exposed to heavy traffic may require thicknesses of 150mm to 200mm or more to prevent premature wear or cracking.
- Average Traffic in Auckland: Auckland experiences a diverse range of traffic in its public and private car parks. In residential areas, car parks are often subject to lighter traffic loads, with most vehicles being personal cars. However, in commercial areas, especially those close to delivery hubs, the traffic load increases due to larger vehicles like trucks. This variation requires different concrete thicknesses based on the specific demands of each location. Additionally, Auckland’s growing urbanization is causing an increase in traffic density, particularly in busy retail and business districts, which may influence future car park designs.
Geological Considerations
The natural ground beneath a car park directly affects the thickness of the concrete required to ensure long-term stability and durability.
- Soil Conditions in Auckland: Auckland has a unique mix of soil types, ranging from clay-rich soils to volcanic rock. Clay soils, in particular, tend to expand and contract with changes in moisture levels, which can cause shifting or cracking in concrete if the foundation isn’t properly prepared. Volcanic rock, on the other hand, provides a more stable base but may still require specific treatment to ensure proper load distribution. Car parks built in areas with softer or more unpredictable soils may need thicker concrete slabs or additional reinforcement to prevent sinking or cracking over time.
- Risk of Earthquakes: While Auckland is located in a low-to-moderate seismic zone, the potential for earthquakes still exists. Seismic activity can exert significant lateral and vertical forces on concrete structures. To account for this, engineers may opt for thicker concrete slabs or additional reinforcement to mitigate the risk of damage during an earthquake. Though the risk is not as pronounced as in other parts of New Zealand, this consideration still plays a part in construction decisions for car parks in Auckland.
Weather and Climate
Auckland’s weather and climate are additional factors that can influence concrete thickness in car parks.
- Impact of Auckland’s Rainy Climate: Auckland is known for its relatively high levels of rainfall, particularly in the winter months. Excessive moisture can cause concrete to expand, contract, or even crack if the structure isn’t adequately prepared. In areas with high rainfall, ensuring proper drainage is essential (as discussed later). Additionally, the concrete itself may need to be thicker or include moisture-resistant additives to prevent water damage, such as cracking or potholing, which can occur over time as water seeps into small fissures in the slab.
- Temperature Considerations: Auckland has a mild climate, but occasional temperature extremes, such as brief heatwaves in the summer or cold snaps in the winter, can affect concrete structures. Temperature fluctuations cause the concrete to expand and contract, which, over time, can lead to cracking. While Auckland doesn’t experience harsh weather conditions, the design of car parks should still account for occasional temperature extremes by using thicker concrete or specialized expansion joints that allow the concrete to flex without cracking.
Drainage Requirements
Proper drainage is essential in car park design, and it can significantly impact the required thickness of the concrete.
- Drainage and Sloping: To prevent water pooling, which can lead to erosion, cracks, or even safety hazards in car parks, an effective drainage system is crucial. Car parks are typically designed with slight slopes to direct water toward drainage systems. The thickness of the concrete must be sufficient to handle both the water runoff and the pressure caused by traffic. If the drainage system is inadequate, water can seep into the concrete, weakening it over time. In Auckland’s rainy climate, this is especially important. By designing the concrete slab to account for water flow, the lifespan of the car park can be significantly extended.
When building car parks in Auckland, several key factors come into play that directly influence the required concrete thickness. Traffic load, soil conditions, seismic activity, weather patterns, and drainage all play crucial roles in ensuring that the concrete slab is strong enough to withstand both daily use and environmental conditions. By carefully considering these factors, engineers and contractors can ensure that Auckland’s car parks remain safe, durable, and functional for years to come.

Standards And Regulations In New Zealand
When it comes to constructing car parks in New Zealand, particularly in cities like Auckland, adhering to national and regional standards is essential. This ensures not only compliance with legal frameworks but also guarantees the safety and longevity of the structures. Let’s take a closer look at how building codes and regional guidelines influence the design and development of car parks in Auckland.
Building Codes in New Zealand
The primary building code that governs construction practices in New Zealand is NZS 3101. This code specifically regulates the design and construction of concrete structures, which is highly relevant for car park developments. NZS 3101 establishes the necessary standards for various aspects of concrete design, including strength, durability, and load-bearing capacities.
For car parks, concrete thickness is a key consideration. The thickness of the concrete slab used in the construction of a car park must be designed to support the weight of vehicles and ensure long service life. NZS 3101 provides detailed guidelines for determining the appropriate concrete thickness based on factors such as:
- Vehicle load: The expected volume and weight of vehicles that will use the parking facility.
- Environmental exposure: Consideration of weather conditions and potential exposure to moisture or chemicals, which can impact the durability of the concrete.
- Structural integrity: Ensuring the concrete slab can withstand not only static loads but also dynamic impacts from moving vehicles.
Following these national standards helps ensure that car parks are constructed safely and effectively, minimizing future maintenance costs and safety risks.
Regional Variations in Auckland
While NZS 3101 sets the overarching national standards, local regulations can introduce additional requirements. In Auckland, the Auckland City Council has specific guidelines that influence the design and construction of car parks. These regional variations can include additional stipulations regarding concrete thickness and other structural elements.
One important aspect of Auckland’s guidelines involves addressing the city’s unique geographical and environmental factors. Auckland’s relatively high levels of rainfall and humidity can accelerate the wear and tear of concrete structures, so developers must ensure that the concrete used in car park construction is capable of withstanding these conditions over time. The Auckland City Council may require approvals and checks to verify that the proposed design meets both national standards and the specific conditions of the region.
Additionally, Auckland’s guidelines might also include provisions for drainage, surface water management, and access routes, all of which indirectly impact the required concrete thickness and structural design of car parks.
Ensuring Compliance
For any car park development project in Auckland, it is essential to comply with both national building codes and the Auckland City Council’s specific guidelines. Typically, this process involves submitting detailed design plans for approval to the council, which will assess whether the car park meets the necessary standards, including those related to concrete thickness. Failing to meet these requirements could lead to costly delays or even the need to redesign the car park.
By adhering to both NZS 3101 and Auckland-specific regulations, developers ensure that the car park will meet all safety, durability, and legal requirements, providing a high-quality facility for its users.
In summary, understanding and implementing the appropriate building codes and local council guidelines is critical for anyone involved in constructing car parks in Auckland. Ensuring compliance with these standards results in safer, more durable car parks that are built to last in New Zealand’s unique environment.
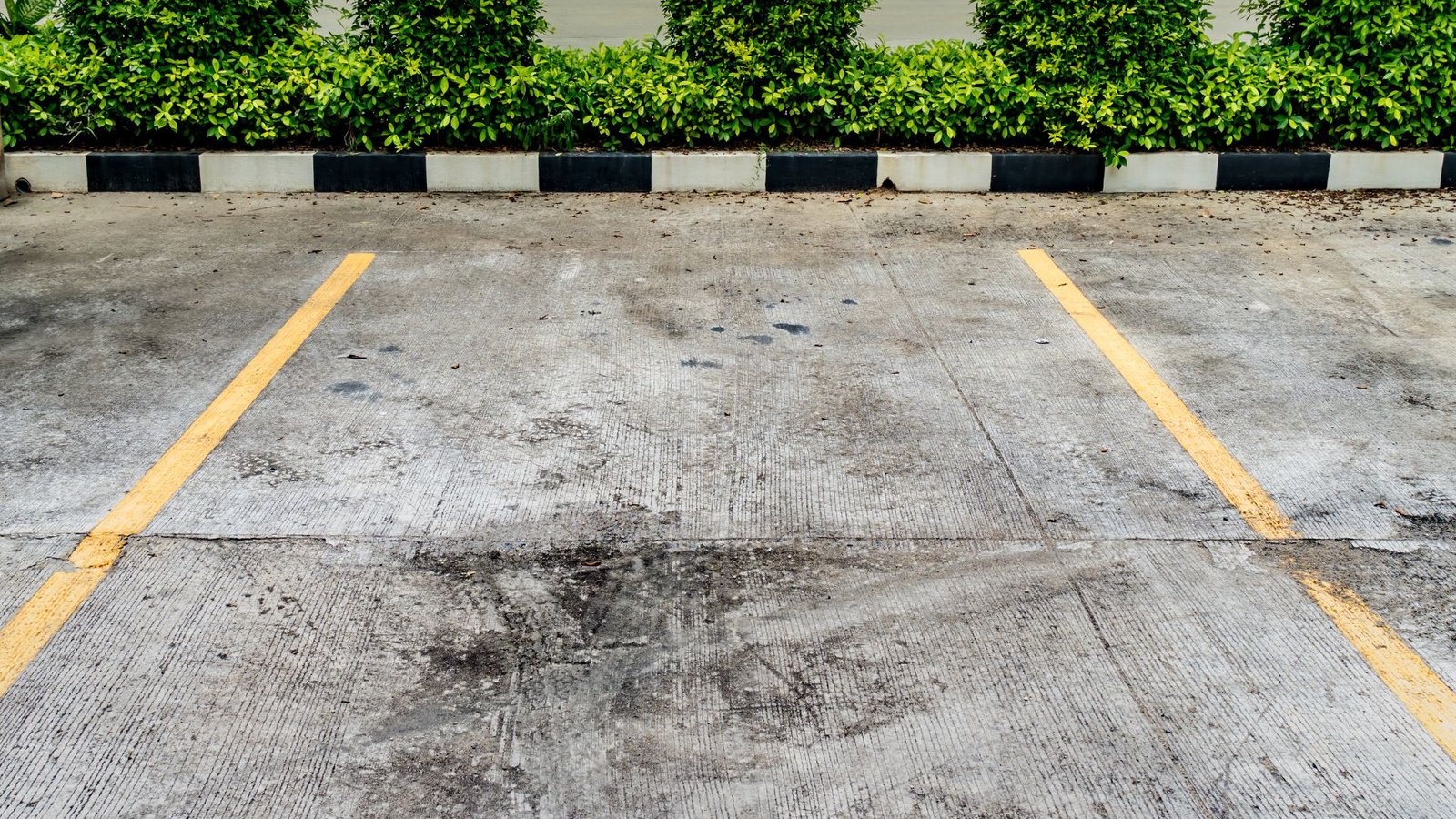
Types Of Concrete Used In Auckland Car Parks
When it comes to building car parks in Auckland, choosing the right type of concrete is crucial. Different types of concrete are selected based on the structural requirements, durability needs, and overall cost-effectiveness of the project. Below are the most common types of concrete used in Auckland car parks and the reasons they are preferred in specific applications.
Standard Reinforced Concrete
Standard reinforced concrete is perhaps the most widely used material in car park construction across Auckland. Its popularity stems from its superior strength and longevity. This type of concrete is reinforced with steel bars, commonly known as rebar, which helps the concrete resist tension and makes it more durable under heavy loads. This is particularly important for car parks, where the surface must withstand constant vehicle traffic, weight, and environmental wear over time.
Reinforced concrete is chosen for car parks not only for its strength but also for its ability to be molded into various shapes and thicknesses, making it versatile for different structural designs. Additionally, it can handle the thermal expansion and contraction caused by Auckland’s varying weather conditions, ensuring that cracks are minimized and the structure remains intact for longer periods. This combination of factors of strength, versatility, and durability makes standard reinforced concrete an ideal choice for car parks across the region.
Fiber-reinforced Concrete
Fiber-reinforced concrete (FRC) is an alternative option that is gaining popularity in car park construction. This concrete type incorporates fibers either synthetic or steel into the mix, which improves its tensile strength and reduces the risk of cracking. Unlike traditional reinforced concrete, where rebar is added after the pour, fibers are mixed directly into the concrete, creating a more evenly distributed reinforcement.
One of the key advantages of fiber-reinforced concrete is that it allows for thinner slabs while still maintaining structural integrity. This can reduce material costs and installation time, making it a cost-effective option for large-scale car parks. Additionally, the use of FRC can enhance the durability of the concrete, especially in areas subject to heavy traffic or where the concrete may be exposed to harsh environmental conditions, such as high moisture or freeze-thaw cycles.
Fiber-reinforced concrete also offers flexibility in design, as the fibers can be tailored to meet specific needs, whether that’s increasing impact resistance, reducing shrinkage, or improving overall toughness. This type of concrete is an excellent choice for car parks that require enhanced durability without the need for excessively thick slabs.
Post-Tensioned Concrete
Post-tensioned concrete is often used in the construction of multi-level car parks, where thinner slabs are necessary to reduce the overall weight of the structure. In this method, steel tendons are embedded in the concrete and tensioned after the concrete has cured. This technique allows the concrete to carry greater loads, making it ideal for car parks with several levels or larger spans that require fewer supporting columns.
The main benefit of post-tensioned concrete is that it creates a more efficient and cost-effective structure. The ability to use thinner slabs reduces material costs, while the increased strength allows for longer spans, providing more open space within the car park. This is particularly advantageous in Auckland, where space can be limited, and maximizing the number of parking spots is often a priority.
Another reason post-tensioned concrete is popular in multi-level car parks is its ability to resist cracking under heavy loads. The tensioned steel tendons provide extra support, helping the concrete withstand the pressures exerted by the weight of vehicles and daily traffic. This reduces the likelihood of cracking or other structural issues that could compromise the car park’s safety or longevity.
In conclusion, the choice of concrete type for an Auckland car park depends on several factors, including the size of the structure, load requirements, and budget. Standard reinforced concrete offers tried-and-tested durability, fiber-reinforced concrete provides flexibility and cost savings with thinner slabs, and post-tensioned concrete is ideal for multi-level designs requiring both strength and reduced weight. Each option brings its unique benefits to the table, making it possible to customize the construction to meet the specific needs of the car park.
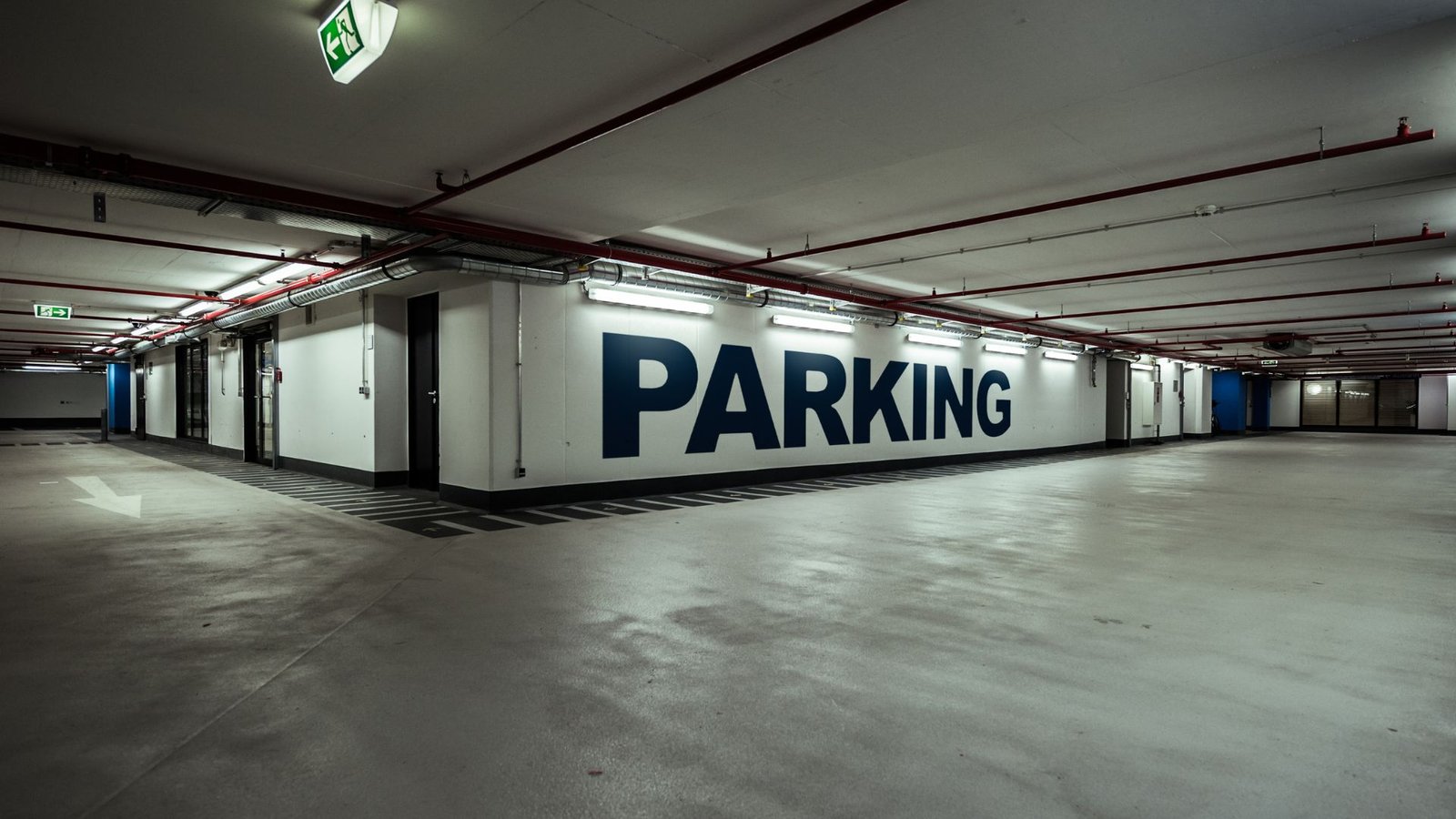
How Is Concrete Thickness Determined For Auckland Car Parks?
Site Assessment and Planning
Determining the appropriate concrete thickness for car parks in Auckland starts with a thorough site assessment. Engineers and construction professionals collaborate to evaluate various factors that will influence the final design. This process typically involves several key steps:
1. Site Surveys: A detailed site survey is the first step. This helps engineers understand the physical characteristics of the area, including elevation, drainage, and potential obstructions. Accurate measurements are essential to plan a layout that optimizes space while ensuring structural integrity.
2. Traffic Analysis: Not all car parks experience the same level of use. Therefore, traffic analysis is vital. Engineers consider the volume and weight of vehicles that will use the space. For example, car parks that accommodate regular car traffic will have different thickness requirements compared to those that need to support heavy vehicles like delivery trucks or buses. This analysis helps in deciding the load-bearing capacity of the concrete slab.
3. Soil Testing: The soil conditions beneath the car park play a crucial role in determining the appropriate thickness. Geotechnical engineers conduct soil tests to assess the load-bearing capacity of the ground. If the soil is weak or prone to movement, the concrete thickness may need to be increased or additional reinforcement added to prevent future cracking or settling.
By thoroughly assessing these factors, engineers can design a car park that is structurally sound and able to handle the unique demands of the site.
Design Considerations
The design phase involves a careful balance between functionality, aesthetics, and cost. Engineers and architects work together to create a layout that not only meets the structural requirements but also provides an aesthetically pleasing and user-friendly space.
1. Functionality: The primary purpose of the car park dictates much of the design. Engineers focus on ensuring that the concrete is thick enough to handle the expected load while optimizing the use of space. The thickness must provide durability while allowing for smooth vehicle movement.
2. Aesthetics: While the primary concern is the structural strength of the concrete, architects also consider how the car park looks. This includes the surface finish, color options, and any features like marking lanes, accessible parking spots, and landscaping elements.
3. Cost Efficiency: One of the main challenges in determining the thickness of the concrete is balancing durability with cost. Thicker slabs are generally more expensive due to the additional materials required. Engineers and builders aim to find a thickness that meets structural standards without unnecessary expenditure.
Overall, the design process ensures that car parks are functional, visually appealing, and built within budget, without compromising safety and durability.
Concrete Pouring and Curing Process
Once the planning and design stages are complete, the actual process of pouring and curing the concrete begins. This stage directly impacts the long-term durability and strength of the car park.
1. Pouring the Concrete: The concrete mix is poured into the prepared site, with the pre-determined thickness based on earlier assessments. Proper pouring techniques are critical to ensuring the concrete is evenly spread and compacted, minimizing air pockets that could weaken the structure over time.
2. Curing Process: After pouring, the concrete undergoes a curing process, where it is allowed to harden and gain strength. Curing usually takes several days to weeks, depending on the weather and environmental conditions. Proper curing is essential to prevent cracks, improve durability, and ensure the concrete achieves its maximum strength potential.
By following these steps, construction teams ensure that the concrete car park is built to withstand daily wear and tear, offering long-term durability with minimal maintenance.
In conclusion, the thickness of concrete for Auckland car parks is a result of meticulous planning, taking into account site conditions, expected traffic, and structural requirements. Through site assessments, design considerations, and careful execution during the pouring and curing process, engineers and builders create car parks that are not only functional and safe but also durable enough to last for years to come.
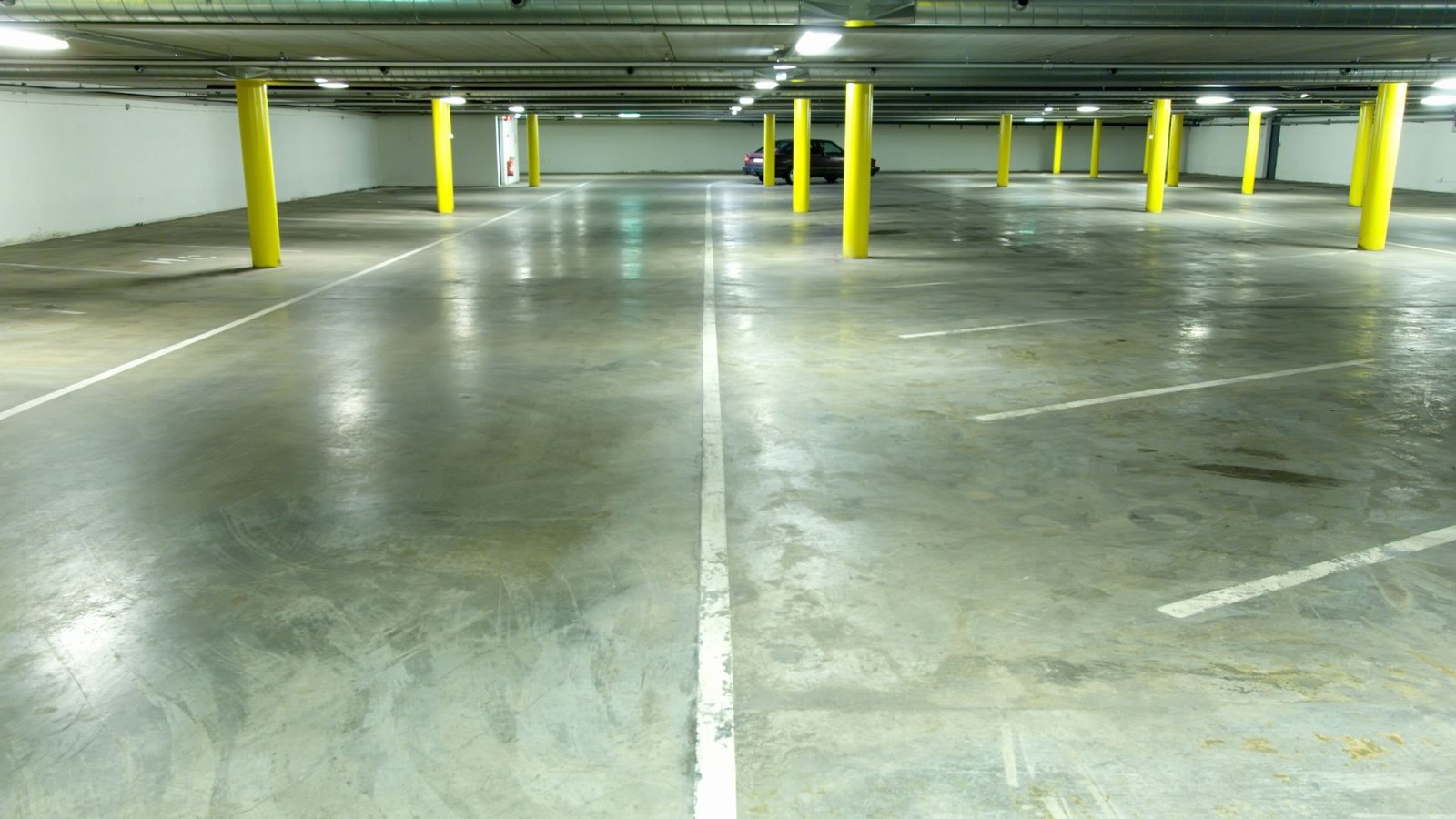
Real-Life Examples: Car Parks In Auckland
Concrete thickness plays a critical role in the longevity, durability, and functionality of car parks. Auckland, being a busy urban environment with a variety of car park types, offers valuable case studies that demonstrate how appropriate concrete thickness is determined based on specific needs. Below, we dive into two real-life examples: a small private car park and a larger commercial or shopping mall car park. Additionally, we’ll explore lessons learned from past projects in Auckland where concrete thickness was a significant factor.
Case Study 1: A Small Private Car Park
A prime example of a small private car park in Auckland involves a residential development with limited space for parking. Typically, these car parks cater to a lower volume of traffic, predominantly light vehicles such as personal cars. In this case, the standard concrete thickness generally ranges between 100mm to 150mm.
Rationale
For a small car park like this, where the traffic load is lighter and less frequent, a concrete thickness of 100-150mm is often sufficient. This thickness provides enough structural support for everyday use without unnecessary costs or excessive material. The environment and expected vehicle types, in this case, dictate the need for moderate thickness, ensuring durability over time while also considering cost efficiency.
In the long term, properly laid concrete with this thickness has proven to resist minor surface wear, cracking, and weathering, common challenges in Auckland’s fluctuating climate. However, proper reinforcement (such as steel mesh) and drainage systems are crucial to ensure the concrete withstands years of use.
Case Study 2: A Commercial or Shopping Mall Car Park
On the other hand, a large-scale commercial car park, like one found at a shopping mall in Auckland, presents significantly different requirements. These car parks are designed to handle much heavier traffic, including delivery trucks and higher volumes of vehicles throughout the day. The concrete thickness in such settings is notably greater, typically ranging from 180mm to 250mm or more.
Rationale
The key consideration here is the increased load and wear that the car park will experience. A thicker concrete slab, often reinforced with steel bars and other structural elements, ensures that the surface can handle repeated stress from heavier vehicles without degrading. In a large commercial car park, the focus is on long-term durability, resistance to cracking, and maintaining an even surface for both safety and user comfort.
Concrete thickness also contributes to minimizing the risk of potholes, surface cracking, and other types of wear that could lead to expensive repairs or downtime, which would be detrimental to a shopping mall’s operations. Additionally, given the volume of vehicles, a well-constructed surface reduces the likelihood of accidents and improves the overall customer experience.
Lessons Learned from Past Projects
Auckland has seen both successful and less-than-ideal car park projects, and the lessons learned from these experiences emphasize the importance of proper concrete thickness.
Success Stories
One well-executed project involved a public parking facility in the city center, where a concrete slab of 200mm was used in conjunction with excellent drainage systems. This project has withstood heavy traffic for over a decade with minimal repairs needed, showcasing how critical proper planning for concrete thickness is in ensuring longevity and reducing maintenance costs.
Failures
Conversely, there have been instances of premature wear and failure, particularly in car parks where the concrete thickness was underestimated. A notable example is a car park that was built with a 100mm concrete slab, despite being intended for mixed vehicle types, including heavy delivery trucks. Within a few years, the car park exhibited significant surface cracks and required costly repairs, disrupting operations and reflecting the importance of selecting the right concrete thickness based on anticipated use.
In conclusion, concrete thickness in Auckland’s car parks is not a one-size-fits-all matter. It requires careful consideration of factors such as traffic volume, vehicle weight, and expected wear over time. Whether in small private car parks or large commercial spaces, the correct slab thickness ensures durability, minimizes maintenance costs, and enhances the overall user experience. The lessons from past successes and failures underscore the value of getting this critical element right from the outset.
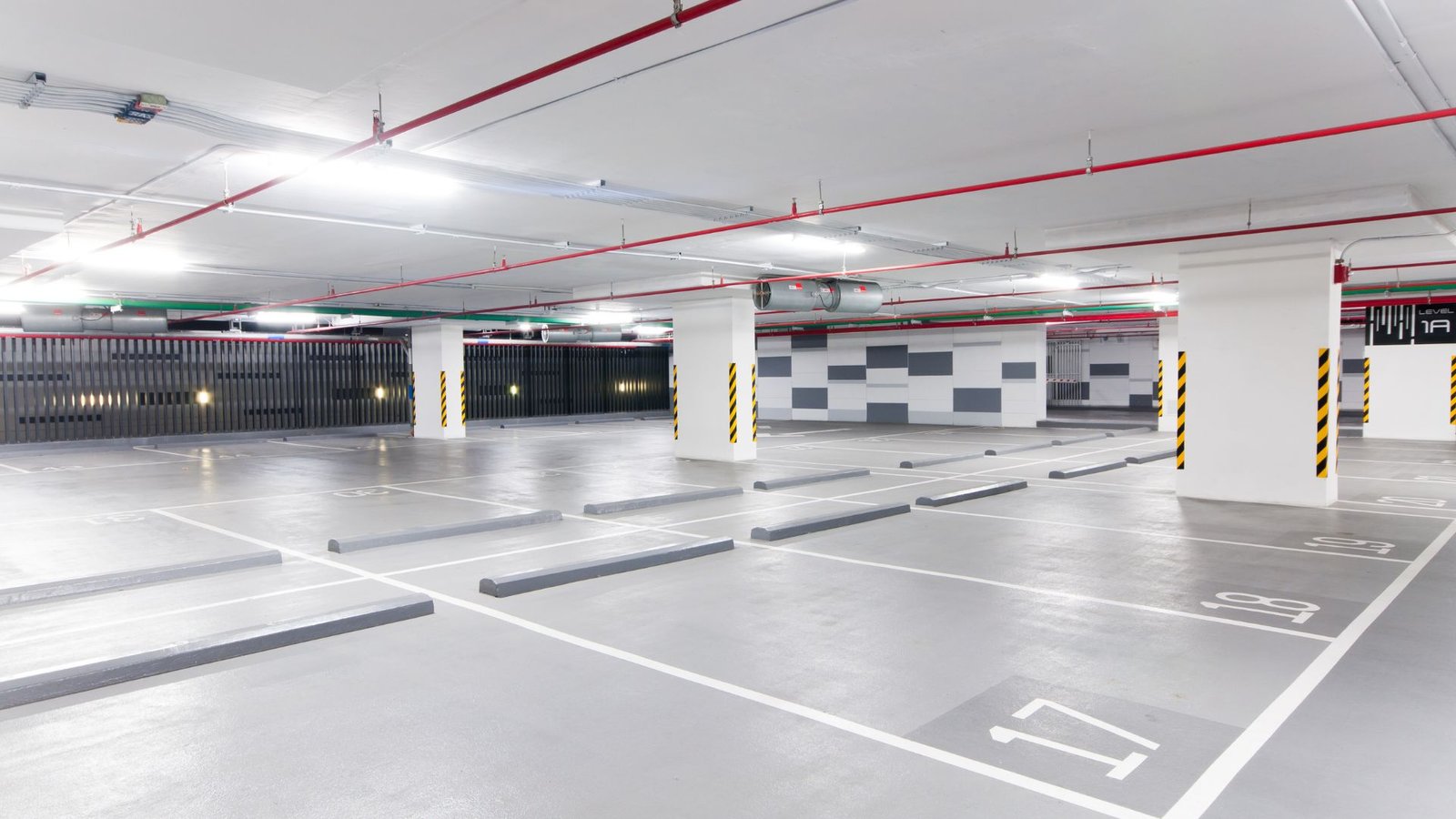
The Cost Factor: Does Thicker Concrete Mean Higher Costs?
When constructing a car park, one of the most significant considerations is balancing quality and cost. The thickness of the concrete plays a pivotal role in this equation. But does opting for thicker concrete automatically mean higher costs? Let’s dive into the details.
Material and Labor Costs
Concrete thickness has a direct impact on both material and labor costs. As the thickness increases, the amount of concrete required naturally goes up. More concrete means you’ll need more raw materials, which can drive up the initial expenditure. Additionally, thicker concrete slabs often require more reinforcement, adding further to material costs.
From a labor standpoint, pouring thicker concrete slabs typically involves more effort and time. The deeper slabs require more precise leveling and finishing, potentially leading to longer work hours for the construction team. This results in higher labor costs, especially when considering the need for skilled workers who can ensure the job is done right. Therefore, while thicker concrete does provide durability, it also involves a heavier investment in both materials and labor.
Long-Term Savings vs. Initial Investment
Although the initial costs of using thicker concrete may seem higher, it’s essential to consider the long-term savings. Thicker concrete is more robust and can handle heavier loads, reducing the chances of cracking, wear, and tear over time. This durability means fewer maintenance and repair costs in the long run.
For instance, a thinner slab might be less expensive upfront but could require more frequent repairs due to its inability to withstand heavy traffic or weathering. Over time, these repairs can add up, potentially surpassing the cost of installing a thicker slab from the start. By investing in the appropriate concrete thickness, you’re likely to extend the life of the car park and avoid costly maintenance down the road.
Balancing Cost and Quality
Finding the right balance between cost and quality is crucial. While it might be tempting to save on the initial construction by opting for thinner concrete, this decision could lead to higher expenses later on. On the other hand, you don’t always need to choose the thickest option available.
Here are a few tips for making the right decision:
1. Assess the traffic load: Consider the type and volume of vehicles that will be using the car park. Heavier or more frequent traffic will require thicker concrete to prevent premature wear.
2. Consult with experts: A professional contractor can guide you on the ideal thickness for your specific project, ensuring you don’t overpay for unnecessary thickness but also don’t compromise on durability.
3. Factor in future usage: If you anticipate an increase in traffic or heavier loads in the future, investing in a slightly thicker slab now can save money in the long run.
4. Budget smartly: Don’t just look at the upfront costs. Weigh the potential for long-term savings against the initial investment to make an informed decision that fits both your budget and long-term needs.
In conclusion, while thicker concrete does mean higher initial costs, it can be a cost-effective solution when you factor in reduced maintenance and increased longevity. Making an informed decision that balances immediate costs with future savings is key to ensuring a durable, long-lasting car park without breaking the bank.
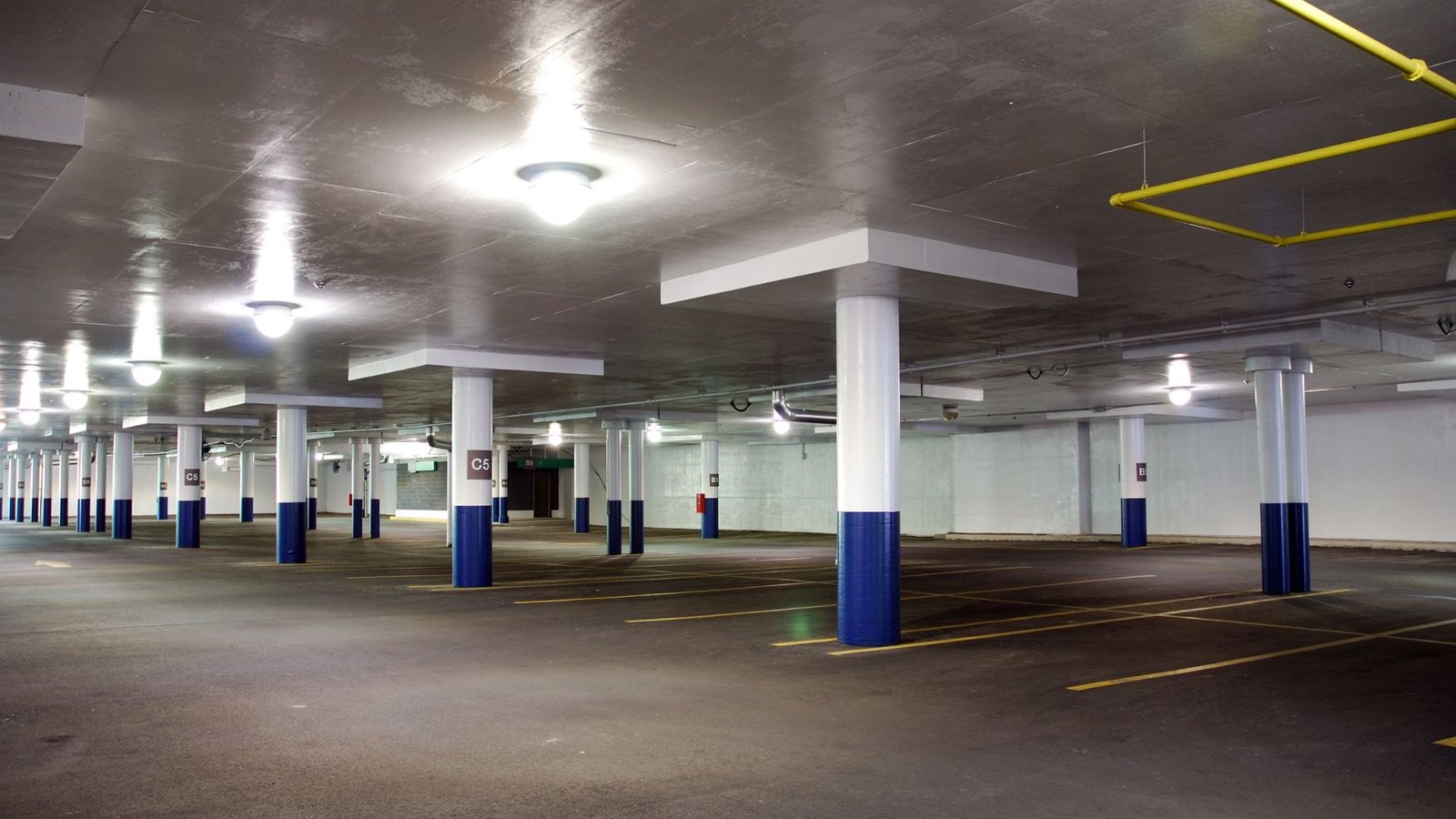
Future Trends In Car Park Construction
In the rapidly evolving world of construction, car park development is no exception. Auckland, like many other cities, is witnessing an increased demand for more efficient, durable, and environmentally friendly car parks. This section delves into two key trends that are shaping the future of car park construction: sustainable concrete solutions and technological advancements.
Sustainable Concrete Solutions: Reducing Environmental Impact
As concerns over climate change and environmental sustainability grow, industries across the board are seeking ways to minimize their carbon footprint. Car park construction is no different, and the use of sustainable concrete solutions is one of the most promising innovations in this field. Traditional concrete production is a major contributor to CO2 emissions, but newer eco-friendly alternatives are being developed to address this issue.
Sustainable concrete practices involve using materials that lower the overall environmental impact without sacrificing strength or durability. One such approach includes incorporating recycled materials, such as fly ash or blast furnace slag, into concrete mixes. These materials reduce the reliance on raw cement, which is the primary source of emissions in concrete production.
Another exciting development is the use of carbon-capturing concrete, which actively absorbs CO2 from the atmosphere. This type of concrete can be used in large-scale projects, including car parks, to help reduce the environmental impact over time. In Auckland, where the city’s carbon neutrality goals are increasingly becoming a priority, adopting sustainable concrete solutions is a step in the right direction for future car park projects.
Technological Advancements: Revolutionizing Construction Techniques
Alongside sustainability, technological advancements are transforming the construction landscape. In the context of car park construction, these innovations are set to enhance efficiency, reduce costs, and improve the quality of the structures.
One of the most groundbreaking advancements is the introduction of 3D printing technology in concrete construction. By using 3D printers to build concrete structures layer by layer, the construction process can be significantly faster and more precise. This method minimizes waste, reduces labor costs, and allows for greater design flexibility key factors in developing future car parks in urban areas like Auckland.
Another notable innovation is self-healing concrete. This material contains embedded microcapsules of healing agents that are released when cracks begin to form. As a result, the concrete can repair itself, preventing small cracks from developing into major structural issues. The use of self-healing concrete could dramatically extend the lifespan of car parks, lowering maintenance costs and improving long-term sustainability.
The future of car park construction in Auckland and beyond is poised to be shaped by two major forces: sustainability and technology. With sustainable concrete solutions reducing environmental impact and technological advancements like 3D printing and self-healing materials revolutionizing construction methods, the industry is set for significant changes. As Auckland grows and continues to prioritize eco-friendly urban development, these trends will likely become the cornerstone of car park projects in the years to come.
By embracing these innovative solutions, Auckland’s car park construction industry can lead the way in creating more sustainable, efficient, and resilient infrastructure, paving the way for a greener future while meeting the demands of urban growth.

FAQs: About How Thick Is The Concrete In A Car Park In Auckland
What is the standard concrete thickness for a car park in Auckland?
The standard concrete thickness for car parks in Auckland generally ranges from 100mm to 200mm. The exact thickness depends on factors like traffic load, soil conditions, and the type of vehicles that will use the car park.
How is the concrete thickness in a car park determined?
Concrete thickness is determined by considering several factors, including the expected traffic load, soil conditions, drainage requirements, and local building codes. Engineers assess the site and determine the appropriate thickness based on these variables to ensure durability and safety.
What is the minimum concrete thickness for light vehicle traffic in Auckland?
For car parks designed for light vehicle traffic, such as personal cars, the minimum recommended concrete thickness is usually around 100mm. This is sufficient to handle the load of standard vehicles while maintaining long-term durability.
Does heavier traffic require thicker concrete in a car park?
Yes, car parks that accommodate heavier traffic, such as delivery trucks or buses, generally require thicker concrete, ranging from 150mm to 200mm. This ensures the concrete can withstand the higher load and stress caused by heavier vehicles.
How does Auckland’s weather affect the thickness of concrete in car parks?
Auckland’s rainy climate and mild temperatures can impact the durability of concrete, especially when considering moisture levels and potential drainage issues. A thicker concrete slab may be required in areas with poor drainage or where constant rain could lead to cracks or surface degradation.
Are there specific regulations for car park concrete thickness in New Zealand?
Yes, car park construction must adhere to New Zealand’s building standards, such as NZS 3101, which governs concrete structures. Auckland-specific guidelines may also apply, especially regarding traffic loads, soil conditions, and weather-related factors.
What types of concrete are used for car parks in Auckland?
Standard reinforced concrete is the most common type used for car parks in Auckland. However, in some cases, fiber-reinforced or post-tensioned concrete may be used for added durability or to reduce the required slab thickness.
Does thicker concrete mean higher construction costs?
Yes, thicker concrete typically leads to higher construction costs due to the additional materials and labor involved. However, investing in the appropriate concrete thickness can save on long-term maintenance and repair costs by preventing cracks or damage caused by insufficient thickness.
Can thin concrete cause problems in a car park?
Yes, if the concrete is too thin for the expected load, it can lead to premature cracking, structural damage, and increased maintenance costs. Ensuring the correct thickness based on traffic and environmental factors is essential to avoid these issues.
How can drainage impact the concrete thickness in a car park?
Poor drainage can lead to water pooling on the surface, which can cause cracking and degradation over time. In such cases, additional thickness may be necessary to ensure the concrete slab can handle the environmental stress and maintain its integrity.
Conclusion
Determining the right concrete thickness for car park construction is crucial for ensuring long-term durability, safety, and cost-effectiveness. For Auckland’s unique conditions, factors such as the weight of the vehicles, soil type, and local climate play significant roles in achieving the ideal balance between strength and affordability. As you consider building or renovating a car park in Auckland, it’s important to consult professionals and prioritize quality materials to prevent costly repairs down the line. If you have any questions, experiences to share, or insights on car park design and concrete thickness, feel free to join the conversation in the comments below.
About the Author:
Mike Veail is a recognized digital marketing expert with over 6 years of experience in helping tradespeople and small businesses thrive online. A former quantity surveyor, Mike combines deep industry knowledge with hands-on expertise in SEO and Google Ads. His marketing strategies are tailored to the specific needs of the trades sector, helping businesses increase visibility and generate more leads through proven, ethical methods.
Mike has successfully partnered with numerous companies, establishing a track record of delivering measurable results. His work has been featured across various platforms that showcase his expertise in lead generation and online marketing for the trades sector.
Learn more about Mike's experience and services at https://theleadguy.online or follow him on social media: